EJ25 failure analysis
Of all the failures that occur in a built engine, the cylinder wall failure is one of the least known/understood…
Conventional wisdom in the Subaru community has told us that you need forged pistons, forged rods, bearings, and you can run 400+ whp on the road course with no issue. We’ve had several mainstream engine builders make this claim and paid thousands of dollars to only have a complete failure at 155+mph on the front straight of Texas World Speedway. The below picture shows the complete catastrophic destruction that is a cylinder wall failure. This engine was a complete loss.
Complete Engine Failure
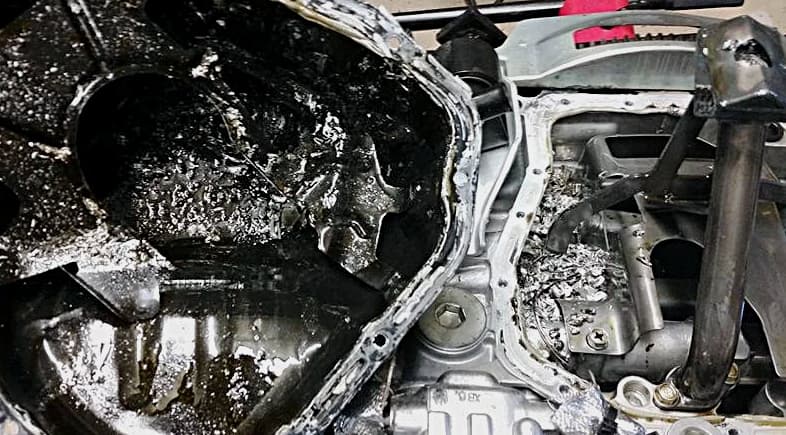
Understanding fatigue and how this impacts cylinder wall failures is key to building a reliable engine. When building an engine at the upper elastic limit of the base material, we find that stress cracking in the cylinder wall becomes more apparent on Road Race cars than any other type due to the nature of the engine having my cycles per time due to high rpm. Stress cracking, fatigue, is a process where cyclic loading causes cracks along the grain boundary of materials. With each cycle (stroke of the piston) the crack propagates (grows) until unexpected failure occurs. Simply put its like taking a paper clip and moving it back and forth with a certain amplitude until it breaks. This process is multiplied when the surface finish is that of a casting, and the material is aluminum. Sound familiar cough cough Subaru 701-702 castings. This is why we limit the horsepower to a lower value as the strain/cycles curve greatly values lowering the stresses by adding more cycles. This is also why you see more and more engine builders pushing for closed deck designs in all applications, or lowering the power in Road Race engines.
Tuning is another massive cause for failures in most engines. If we were to pick a single cause for most of the engine failures in the Subaru community, it would be from a bad tune, or from not getting a tune when mods were added. Simply put, knock is like taking a hammer to the top of your piston, cylinder wall, and valves all at the same time. The stresses exerted by a knock event during a high boost scenario will greatly limit the life of your motor. This is why you see many of the cast pistons breaking on the weakest point; the ringlands. To be fair to Subaru, we understand that if the failure didn’t occur at the ringlands it would surely occur at the cylinder wall.
As we said previously the location for these failures on built motors is the cylinder wall. Admittedly, we aren’t the first to understand and try to correct this inherent design flaw, but we surely have the best design; meant to reduce cylinder temperatures while keeping your casting in one piece. Below is an analysis we did for the EJ25 motor under race conditions. Referring to the above picture of the total’d motor, it is easy to see the high stress areas on the cylinder wall and the resultant failure. A common “fix” for this problem is to install a press-fit insert into the upper portion of the short block – where the highest stresses occur. But this creates another problem; cylinder hot-spotting.
Cylinder hot-spotting occurs when the coolant is not able to reach the cylinder wall, and thus carry the heat to the radiator. Unfortunately, due to the nature of the closed decking process, this is a necessary evil. The insert is press fit around the cylinder to help support it during operation, so how do we alleviate this smaller, still important problem of hot spotting? We have created a press fit insert as seen below, that has an increased surface area on the bottom to allow for higher rates of heat transfer. Much like a heat exchanger, or radiator works by adding fins to create more surface area, we created small valleys in the insert material so coolant can flow. Our analysis has shown this to reduce cylinder temperatures by as much as 15% and inherent stresses in the block by 5%. As far as we’re aware, we are the first to do this, and are excited to announce this in all of our motors.
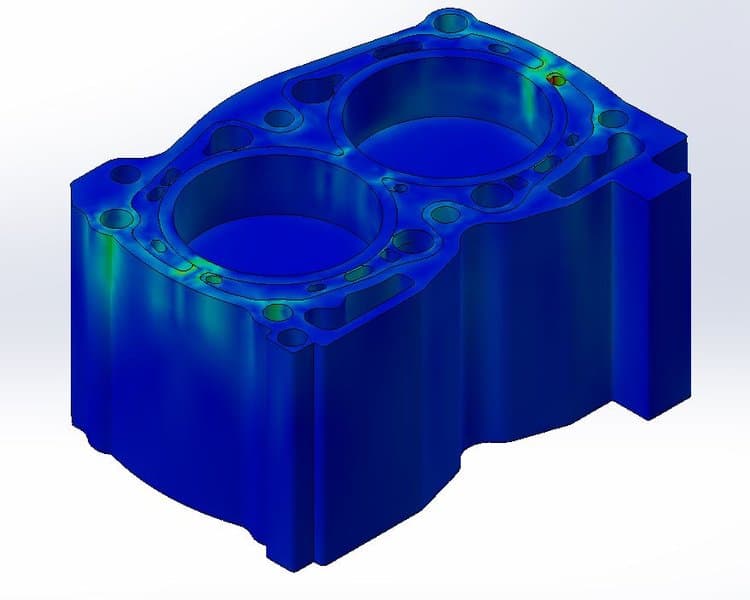
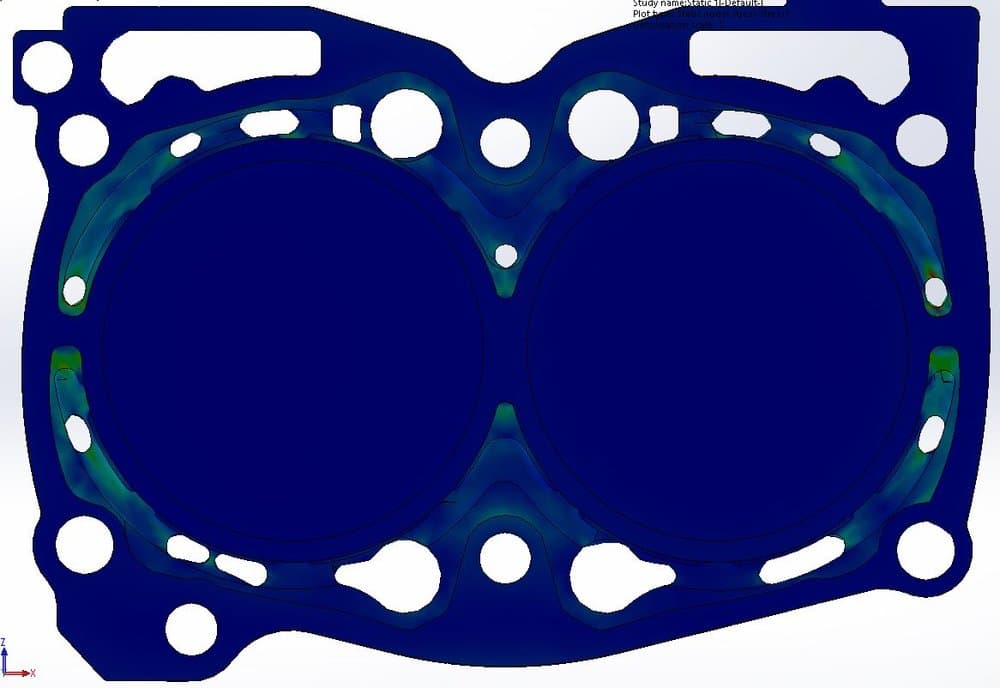